Weeks at work with the Ekobot weeding robot
During weeks in May, June and July of 2022, many hours have been spent by ducksize with Ekobot weeding robot. This was the first time for Ekobot to perform weeding in a 2.5 hectares onion field over the complete growth season in The Netherlands. Here you can read an impression about how the Ekobot robot works, based on experience.

What does the Ekobot robot do?
The Ekobot robot is removing weeds at an onion field, by automatic mechanical strikes. It's using a fully self-driving platform, therefore the Ekobot robot is able to perform the weeding job autonomously.
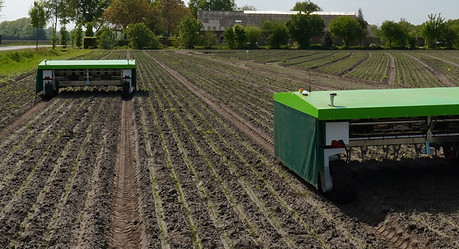
What are benefits from the Ekobot robot?
Essential benefits from the Ekobot robot are:
-
More onion harvest by using less chemicals, for conventional farmers. As less ('contact spray') chemicals are needed, to keep the field without weed.
-
No intensive labour needed to remove weed from the onion field, for ecological farmers.
-
Enable better onion growth, since weeds are continuously being removed from the onion field.
-
Weeding by electrical power, since the platform is not using an fossil fuels.

What is the weeding performance?
Over the entire weeding period, the weeding performance has been measured by Wageningen University and Research. The performance of the Ekobot robot:
-
97% of weed removed
-
Less than 0,5% onions hit (lower couldn't be measured)
Ekobot weeding mechanism
There is a line of cameras mounted below the Ekobot. The cameras keep an eye on the onions to detect if there is any weed. The steps to remove the weed are as following:
-
Camera spots the weed
-
Arm will get near the weed, to prepare strike
-
Arm performs a strike, resulting in the weed removal
These steps are shown in sequentially in the three photos below. During this operation, the robot continues to drive. The arms can strike both in left and right directions. The arm cover a wide area, therefore they can help each-other. For example, when one row is very weed-intensive, two arms will be able to remove weed there. In this way, the robot can perform thousands of strikes per hour.
​

<- camera spots this weed

<- arm gets near the weed

removed by strike ->
What is the overall Ekobot performance?
The robot did an impressive job, simply by what it has to do: Striking weed and not striking onions. In terms of capacity it is intended to cover a 10 hectares field, fully autonomously. Within the current set-up, obviously the machine had a significant over-capacity on the 2.5 hectares field. Therefore, seems promising. However, in the current set-up, batteries needed to be charged after a day of operating. Therefore, batteries may need to become swap-able. Additionally, it would be great if safety systems could be upgraded to allow fully autonomous drive.
​
Opinion about Ekobot, by Corné Rispens:"Meanwhile I was being busy to shoot photos, check the actual field result, learning myself how to set-up the path planning and learn advanced ways for monitoring .... the weeding season was over faster than expected. There were no boring times, sitting 'as a duck' on the side of the field.... and for next years, I would expect it's likely that boring moments will happen for an operator (and that's very good news).
​
What did impress me most? Two things to mention: First, when switching to a new onion-field, the cameras did NOT need any configuration to perfectly detect the onions and weeds. This robots does NOT require any configuration in terms of row-distance, because the detection of onions is simply that good.
And the second thing that highly impressed me was the ability to implement fixes at a high pace, remotely from Sweden. This was for example done when new objects like fertilizer was detect and also when something on the remote control wasn't perceived user friendly, the fixes where implemented and operational in a matter of minutes to hours by the team in Sweden"
A big thanks to ...
This experience has been made possible by the enthusiasm and hospitality of Gijs and Paul Krol.
On the field, thankful for the collaboration was together with Jules Beckers and Jeroen de Bruin.
And, almost needless to say, a big shout out to the entire Ekobot team. With sometimes on-site and mainly remotely providing committed support during test.

More about Ekobot?
Ekobot is a frontrunner for advanced technology for agriculture, as shown with this robot. The company is based in Sweden. Discover more about Ekobot and their contact info, at the product page.
​
If you've any questions about this robot or suggestions to report on at this website, please don't hesitate to send a message to ducksize.

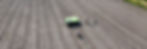